Syncrude Fluid Coker Facility Repair
Client:
Mildred Lake, Alberta, Canada
Syncrude Canada Ltd.
Location:Mildred Lake, Alberta, Canada
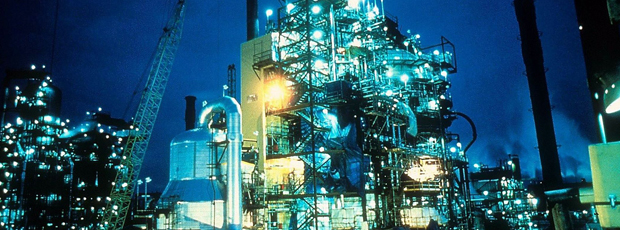
A massive fire at Syncrude’s oil sands upgrading plant near Fort McMurray caused
extensive damage to the coking facility and shut down the entire plant. Loss of
the 80,000 barrel-a-day plant cost Syncrude over $2.5 million revenue loss per day.
The disaster repair was the critical schedule driver.
Fluor was at work with less than 24-hours' notice to help with emergency repairs.
Fluor provided project management, engineering, procurement, construction, materials control, and startup services to get the plant operational.
In addition to the fire-damage project, Syncrude took the opportunity to make changes to the oil-sands operation to increase site performance and reliability. One third of the work was new design, including modernizing the technology on Coker Unit No.2.
Fluor was at work with less than 24-hours' notice to help with emergency repairs.
Fluor provided project management, engineering, procurement, construction, materials control, and startup services to get the plant operational.
In addition to the fire-damage project, Syncrude took the opportunity to make changes to the oil-sands operation to increase site performance and reliability. One third of the work was new design, including modernizing the technology on Coker Unit No.2.
Client's Challenge
A massive fire shut down Syncrude’s entire oil sands upgrading plant. Loss of the
80,000 barrel-a-day plant cost Syncrude over $2.5 million revenue loss per day.
Syncrude needed a company with expertise in fire rebuilds to get the critical plant
back in operation in a timely manner.
Fluor was at work with less than 24-hours’ notice to help with emergency repairs.
Fluor mobilized a team to the site within five days to assess the damage and develop a plan to rebuild the damaged facilities.
Fluor also assisted Syncrude in preparing estimates for the insurance claim. Utilities at the plant were back in operation in 100 days, and feed was reintroduced to the coker five months after the incident.
Fluor provided project management, engineering, procurement, construction, materials control, and startup services to get the plant operational.
Syncrude managed the overall construction effort, negotiated all contracts, awarded, and administered them.
Fluor was at work with less than 24-hours’ notice to help with emergency repairs.
Fluor mobilized a team to the site within five days to assess the damage and develop a plan to rebuild the damaged facilities.
Fluor also assisted Syncrude in preparing estimates for the insurance claim. Utilities at the plant were back in operation in 100 days, and feed was reintroduced to the coker five months after the incident.
Fluor provided project management, engineering, procurement, construction, materials control, and startup services to get the plant operational.
Syncrude managed the overall construction effort, negotiated all contracts, awarded, and administered them.
Solution
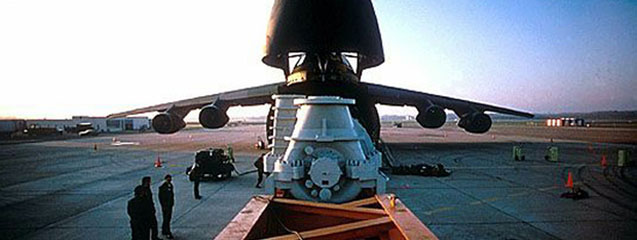
The plant suffered extensive fire damage.
Fluor mobilized a team to Syncrude’s facilities to assess the damages, develop a plan for rebuilding the damaged facilities, and assist Syncrude prepare estimates for the insurance claim.
To meet the Client’s urgent schedule recovery, Fluor mobilized resources from multiple locations, not just Fluor Canada.
Fluor developed an abbreviated schedule that encompassed 230,000 staff work hours and 210,000 craft hours. One timesaving innovation was moving the home office to the field. Fluor had both day and night shift construction crews engaged. Fluor incorporated all repair work and activities of 1,700 construction tradespeople.
One third of the project included plant improvements; the balance of work involved replacement in kind.
Fluor’s scope included planning, engineering, procurement, and construction that would be performed in parallel. Fluor’s scope of facilities also included construction of the electrical and instrumentation works and insurance claim support. Separate construction activities, which normally are phased, were performed simultaneously as well. Engineering took place at the jobsite and included both repair work and debottlenecking to improve coker capacity. Computers were used at the jobsite to track field progress, engineering, material control, finance and payroll.
Fluor performed all procurement worldwide, which required that long-lead delivery items such as chrome piping, fittings, and valves be at the plant site in 10 weeks. The long lead times involved in fabrication demanded that major components damaged in the fire be re-built rather than re-ordered. The damaged units were trucked thousands of miles to waiting vendors for immediate rebuilding.
However, most of the repairs required the unit return to Alberta came after the onset of winter. The search was on for alternative transportation that would minimize the risks and delays of blizzards and icy roads.
Fluor originated the idea to utilize the military aircraft. Through the innovative combination of efforts encompassing Syncrude’s and Fluor’s government liaisons in Ottawa and Washington D.C., U.S Air Force C5-A Galaxy and Hercules planes made five separate airlifts delivering the components. The large–scale equipment included the off- gas compressor unit and the lower half of the air blower. Another impressive part of the effort required Fluor to act as air traffic control to land the components to the job site.
Fluor mobilized a team to Syncrude’s facilities to assess the damages, develop a plan for rebuilding the damaged facilities, and assist Syncrude prepare estimates for the insurance claim.
To meet the Client’s urgent schedule recovery, Fluor mobilized resources from multiple locations, not just Fluor Canada.
Fluor developed an abbreviated schedule that encompassed 230,000 staff work hours and 210,000 craft hours. One timesaving innovation was moving the home office to the field. Fluor had both day and night shift construction crews engaged. Fluor incorporated all repair work and activities of 1,700 construction tradespeople.
One third of the project included plant improvements; the balance of work involved replacement in kind.
Fluor’s scope included planning, engineering, procurement, and construction that would be performed in parallel. Fluor’s scope of facilities also included construction of the electrical and instrumentation works and insurance claim support. Separate construction activities, which normally are phased, were performed simultaneously as well. Engineering took place at the jobsite and included both repair work and debottlenecking to improve coker capacity. Computers were used at the jobsite to track field progress, engineering, material control, finance and payroll.
Fluor performed all procurement worldwide, which required that long-lead delivery items such as chrome piping, fittings, and valves be at the plant site in 10 weeks. The long lead times involved in fabrication demanded that major components damaged in the fire be re-built rather than re-ordered. The damaged units were trucked thousands of miles to waiting vendors for immediate rebuilding.
However, most of the repairs required the unit return to Alberta came after the onset of winter. The search was on for alternative transportation that would minimize the risks and delays of blizzards and icy roads.
Fluor originated the idea to utilize the military aircraft. Through the innovative combination of efforts encompassing Syncrude’s and Fluor’s government liaisons in Ottawa and Washington D.C., U.S Air Force C5-A Galaxy and Hercules planes made five separate airlifts delivering the components. The large–scale equipment included the off- gas compressor unit and the lower half of the air blower. Another impressive part of the effort required Fluor to act as air traffic control to land the components to the job site.
Conclusion
Fluor mobilized a rapid response team to quickly assess the damages at the Syncrude
plant. After preparing a detailed plan to rebuild the facility, engineers and construction
workers assembled at the jobsite to begin reconstruction of the damaged facilities.
Fluor implemented a comprehensive safety program that yielded a low accident record
in spite of severe weather and extremely congested conditions.
Fluor was successful in assisting the Client with emergency repairs and in concert, modernizing the technology on the Coker Unit No. 2. Fluor developed stringent quality control procedures to test plant equipment, which led to a trouble-free start-up.
After the project was completed, the plant capacity improved to 87,000 barrels per day, an increase of 7,000 barrels from pre-fire capacity.
This fast-track project was executed entirely at the jobsite and took 116 days to reach project completion.
Syncrude was very satisfied with the quality of Fluor’s emergency response and selected Fluor to perform similar follow-on work on another unit in Alberta.
Read about other Fluor Constructors projects.
Fluor was successful in assisting the Client with emergency repairs and in concert, modernizing the technology on the Coker Unit No. 2. Fluor developed stringent quality control procedures to test plant equipment, which led to a trouble-free start-up.
After the project was completed, the plant capacity improved to 87,000 barrels per day, an increase of 7,000 barrels from pre-fire capacity.
This fast-track project was executed entirely at the jobsite and took 116 days to reach project completion.
Syncrude was very satisfied with the quality of Fluor’s emergency response and selected Fluor to perform similar follow-on work on another unit in Alberta.
Read about other Fluor Constructors projects.